Our main products: Amino silicone, block silicone, hydrophilic silicone,all of their silicone emulsion,wetting rubbing fastness improver, water repellent(Fluorine free,Carbon 6,Carbon 8), demin washing chemicals(ABS, Enzyme, Spandex protector, Manganese remover), Main export countries: India, Pakistan, Bangladesh, Türkiye, Indonesia, Uzbekistan, etc
Application of Dispersed Dye Leveling Agent in Dyeing and Polyester
Disperse dyes are mainly used for dyeing hydrophobic fibers such as polyester, spandex, nylon, and acetate fibers. With the continuous advancement of fiber dyeing technology, various types of leveling agents have made significant progress.
1、 Leveling agent for high-temperature dyeing
When using dispersed dyes for high-temperature and high-pressure dyeing, uneven dyeing is often caused by factors such as poor dispersibility, uniformity, and transfer of the dye, as well as improper control of heating rate. Especially for fine polyester fibers, the linear density is very low, the surface area increases, and the dyeing speed of dyes accelerates. In addition, the tight fabric structure makes it difficult for dyes to penetrate, resulting in more prominent dyeing unevenness than conventional polyester fibers. The use of high-temperature dispersing leveling agents during dyeing can improve the leveling effect of fabrics and enhance product quality.
Generally, non-ionic surfactants can be used as leveling agents for non-ionic dispersed dyes, which can form hydrophobic bonds and slow down the dyeing speed to achieve leveling. Among non-ionic dispersing leveling agents, polyoxyethylene ester surfactants have better leveling performance than polyoxyethylene ether surfactants (ester structures have a greater affinity for polyester than ether structures), and surfactants with benzene rings have better leveling performance than fatty surfactants.
However, non-ionic surfactants are prone to dehydration during high-temperature dyeing of polyester, and the binding between ethylene oxide chains and hydroxyl, amino, and other functional groups in dye molecules is physically loose adsorption, lacking ion interaction forces and poor dispersibility and solubilization. When using low cloud point non-ionic surfactants, dye aggregation is highly likely to occur. Due to the strong negative charge layer formed by the adsorption of anionic surfactants on the surface of dye particles, there is a strong electrical repulsion between dye particles to form a stable dispersed state, which has a strong dispersing ability on the agglomerates of dispersed dyes, thereby reducing their cohesiveness and keeping the dye stable in the dye solution. This can solve the problem of dye spots caused by low cloud point of nonionic surfactants.
A high-performance high-temperature leveling agent is formulated by utilizing the synergistic and synergistic effects of non-ionic and anionic surfactants, where the different structures of each component have different effects. There are many high-temperature leveling agent products (some of which also include some carriers) formulated with anionic/nonionic surfactants. The different structures of each component have different functions, mainly divided into: 1) ethoxy structure can capture dispersed dyes, increase dye sites, and delay dyeing during the dyeing process; 2) When the dyeing temperature reaches a critical value, aromatic compounds can rapidly cause plasticization and swelling of polyester fibers, reducing the glass transition temperature of polyester by 20-25 ℃, significantly increasing the pores inside the fibers, and allowing dyes to quickly and concentratedly dye the fibers. At the same time, they can act as solvents for dyes to continuously desorb and detach from the fibers, resulting in significant migration (transfer dyeing) to achieve uniform dyeing effect.
Some of the complex products of surfactants have high foaming properties, which can easily cause problems in rapid dyeing machines and small bath dyeing. Therefore, low foaming leveling agents are required. The solution is to add defoamers, especially organosilicon defoamers, which are very effective at high temperatures; Low foaming products are obtained by copolymerizing ethylene oxide and propylene oxide.
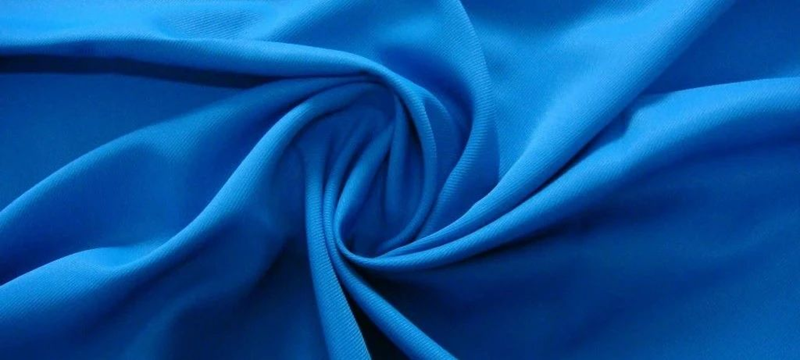
2、 Leveling agent for hot-melt dyeing
Disperse dyes often experience migration during the hot melt dyeing process, resulting in defects such as color spots, positive and negative surfaces, and streaks on the fabric surface, causing uneven dyeing. To solve this problem, it is necessary to use anti swimming agents. There are currently two types of anti swimming agents used: one is sodium alginate; The other type is copolymers of acrylic acid. Sodium alginate has poor uniformity, while acrylic copolymer has good anti migration ability and no staining phenomenon.
Post time: Oct-24-2024